With the continuous development of industrial manufacturing technology, zinc alloy is widely used in various fields because of its excellent performance. In the processing of zinc alloy products, polishing and deburring is a crucial step, which directly affects the appearance quality and service life of the products. In this paper, we will discuss the method and application of zinc alloy polishing and deburring.
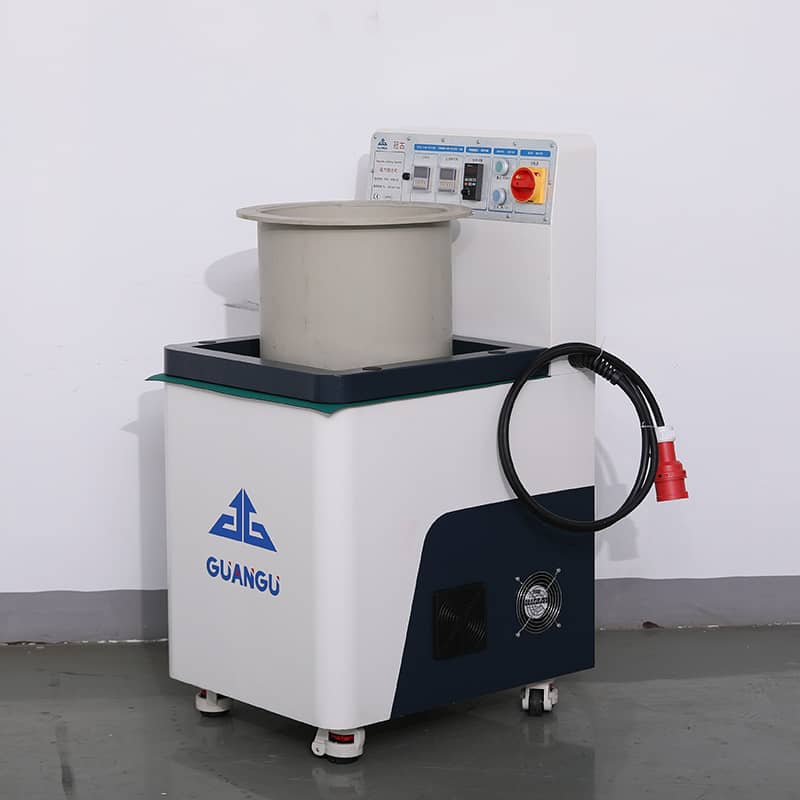
I. Properties and application fields of zinc alloy
Zinc alloy is a zinc-based alloy material, with good casting performance, compressive strength and corrosion resistance. Because of its unique properties, zinc alloy is widely used in automobile, electronics, hardware, construction and other industries. With the progress of science and technology, the application of zinc alloy is still expanding, the quality of zinc alloy products is also more and more demanding.
Second, the importance of zinc alloy polishing deburring
Zinc alloy products in the casting, processing will produce certain burrs and dirt, these burrs and dirt will affect the appearance of the product quality, and may even lead to product failure in the use of the process. Therefore, it is crucial to polish and deburr zinc alloy products. Polishing and deburring not only improves the appearance of the product, but also ensures the safety and reliability of the product in the process of use.
Third, zinc alloy polishing deburring method
- Manual polishing
Hand polishing is a traditional polishing method, mainly through manual operation of polishing cloth, polishing paste and other tools for zinc alloy products. Manual polishing has the advantages of simple operation and strong flexibility, but the efficiency is low and the requirements for polishing personnel are high. In actual production, manual polishing is mainly used for small or complex shape zinc alloy products.
- Mechanical polishing
Mechanical polishing is the use of polishing machines, polishing wheels and other equipment for polishing zinc alloy products. Mechanical polishing has high polishing efficiency and is suitable for mass production. According to the different polishing machines, mechanical polishing can be divided into dry polishing and wet polishing. Dry polishing is suitable for zinc alloy products with low surface requirements, while wet polishing is suitable for zinc alloy products with high surface requirements.
- Chemical polishing
Chemical polishing is the use of chemical reactions to polish zinc alloy products. Chemical polishing has the advantages of fast speed and good effect, but it should be noted that chemical polishing has higher requirements on the material and surface of zinc alloy, and is only applicable to specific zinc alloy products. In addition, the waste liquid generated during the chemical polishing process needs to be properly disposed of to minimize the impact on the environment.
- Electroplating polishing
Electroplating polishing is the polishing of zinc alloy products through the electroplating process. Electroplating polishing has the advantages of bright surface and good corrosion resistance, which is suitable for the production of high-grade zinc alloy products. However, electroplating polishing equipment investment is large, the production cost is high, suitable for mass production.
Fourth, conclusion
In short, zinc alloy polishing deburring is a key step to ensure product quality and safety. In actual production, according to the requirements of the product and production scale, you can choose the appropriate polishing method. With the progress of science and technology, zinc alloy polishing deburring technology is also constantly updated and developed, contributing to the prosperity of the zinc alloy industry.
You must be logged in to post a comment.